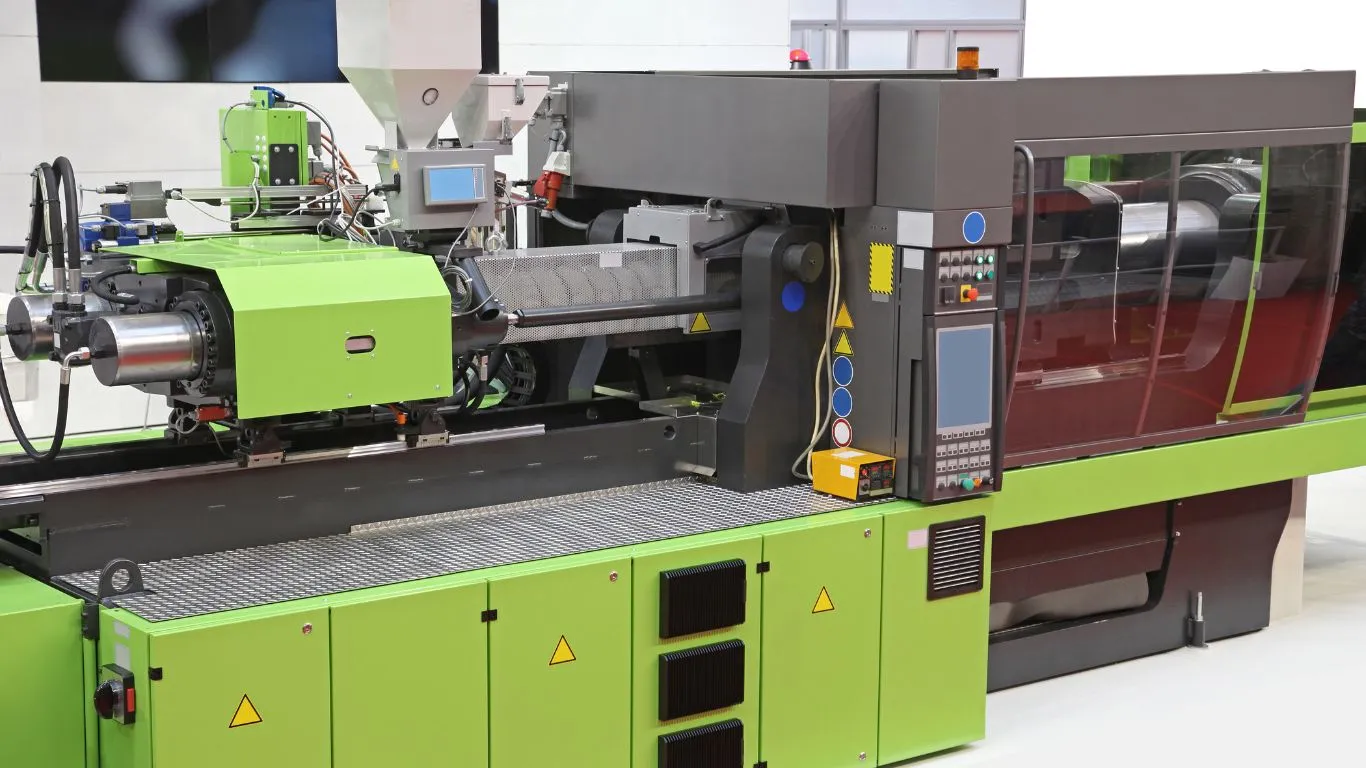
Inhaltsverzeichnis
- Einleitung: Was sind Spritzgussteile?
- Grundprinzip des Spritzgusses
- Materialauswahl für Spritzgussteile
- Thermoplaste
- Duroplaste
- Elastomere
- Schritt-für-Schritt-Herstellungsprozess von Spritzgussteilen
- Trocknen des Kunststoffgranulats
- Einspritzen des Kunststoffs
- Kühlphase
- Entformung und Nachbearbeitung
- Verwendung und Anwendungsgebiete von Spritzgussteilen
- Vorteile des Spritzgussverfahrens
- Herausforderungen und Grenzen des Spritzgusses
- Werkzeugbau für Spritzgussformen
- Qualitätssicherung bei der Produktion von Spritzgussteilen
- Innovationen im Bereich Spritzgussverfahren
- Umweltaspekte und Recycling von Spritzgussteilen
- Kostenfaktoren im Spritzgussprozess
- Die Zukunft des Spritzgießens: Trends und Entwicklungen
- Fazit: Bedeutung und Nutzen von Spritzgussteilen
- FAQs zu Spritzgussteilen
Einleitung: Was sind Spritzgussteile?
Spritzgussteile sind Kunststoffteile, die mithilfe des Spritzgussverfahrens hergestellt werden. Dieser Prozess ermöglicht die Produktion von Bauteilen in großer Stückzahl, die dabei äußerst präzise, stabil und kosteneffizient gestaltet sind. Spritzgussteile sind allgegenwärtig und finden sich in zahlreichen Produkten des täglichen Lebens, von Automobilteilen und Elektronik bis hin zu Spielzeugen und medizinischen Geräten. Doch wie funktioniert das Verfahren genau? Lassen Sie uns einen detaillierten Blick darauf werfen.
Grundprinzip des Spritzgusses
Das Spritzgussverfahren basiert darauf, Kunststoff in einem thermoplastischen Zustand in eine Form zu pressen, wo er anschließend abkühlt und erstarrt. Durch das präzise Design der Form erhält das fertige Teil seine genaue Form und Struktur. Dieses Verfahren eignet sich besonders für die Herstellung komplexer und präziser Teile, da die Formen mit extrem hoher Genauigkeit hergestellt werden können.
Materialauswahl für Spritzgussteile
Die Auswahl des geeigneten Materials ist im Spritzgussverfahren entscheidend. Grundsätzlich werden Kunststoffe in drei Hauptgruppen eingeteilt:
Thermoplaste
Thermoplaste wie Polyethylen, Polypropylen oder Polystyrol sind Kunststoffe, die sich bei hohen Temperaturen verformen lassen und nach dem Abkühlen wieder in eine feste Struktur zurückkehren. Sie sind weit verbreitet im Spritzguss, da sie mehrmals eingeschmolzen und geformt werden können.
Duroplaste
Duroplaste, wie Epoxidharze und Phenolharze, härten während des Produktionsprozesses aus und lassen sich anschließend nicht mehr umformen. Diese Materialien sind besonders für Anwendungen geeignet, die hohe Temperatur- und Formstabilität erfordern.
Elastomere
Elastomere sind flexible Materialien, die sich leicht verformen lassen und ihre Form wieder annehmen, wie beispielsweise Gummi. Sie werden oft in der Herstellung von Dichtungen und Dämpfungen verwendet.
Schritt-für-Schritt-Herstellungsprozess von Spritzgussteilen
Trocknen des Kunststoffgranulats und mögliche Defekte
Bevor das Kunststoffgranulat in den Spritzgussprozess eingegeben wird, ist eine sorgfältige Trocknung notwendig. Kunststoffe, insbesondere hygroskopische Materialien wie Polyamid oder Polycarbonat, neigen dazu, Feuchtigkeit aus der Luft aufzunehmen. Wenn das Granulat nicht ausreichend getrocknet wird, können verschiedene Qualitätsprobleme entstehen:
- Schlierenbildung auf der Oberfläche: Feuchtigkeit, die im Granulat verblieben ist, kann während der Erhitzung im Spritzgussprozess verdampfen und dabei Schlieren oder unregelmäßige Muster auf der Oberfläche des fertigen Teils hinterlassen. Diese optischen Defekte beeinträchtigen nicht nur das Aussehen, sondern können auch die mechanische Integrität des Bauteils beeinflussen.
- Lufteinschlüsse und Porosität: Restfeuchte führt zu Dampfentwicklung, die kleine Bläschen oder Hohlräume im Kunststoff verursacht. Diese Blasen können die strukturelle Stabilität beeinträchtigen und in kritischen Anwendungen zu Schwachstellen führen.
- Nicht vollständig ausgefüllte Teile: Ein zu hoher Wassergehalt im Granulat kann die Viskosität des Kunststoffs verändern, wodurch es schwieriger wird, die Form vollständig auszufüllen. Infolgedessen können Teile unvollständig oder mit ungleichmäßiger Dichte gefertigt werden, was sie für die Verwendung ungeeignet macht.
Um diese Defekte zu vermeiden, wird das Kunststoffgranulat vor dem Einspritzen in speziellen Trocknungsanlagen getrocknet. Die Trocknungszeit und -temperatur variieren je nach Material, sind jedoch entscheidend, um das bestmögliche Ergebnis zu erzielen.
Einspritzen des Kunststoffs: Homogenisierung, Additive und Farbzugabe
Nach der Trocknung wird das Granulat in die Spritzgießmaschine eingeführt. Hier findet die Homogenisierung und Aufschmelzung des Materials in einer beheizten Schnecke statt. Dieser Prozess ist für die gleichmäßige Verteilung von Temperatur, Druck und Additiven von großer Bedeutung.
- Homogenisierung des Kunststoffs: Die Schnecke, die sich in einem Zylinder bewegt, sorgt durch ihre rotierenden Bewegungen dafür, dass das Granulat gleichmäßig aufgeschmolzen und zu einer homogenen Masse vermischt wird. Durch das kontrollierte Mischen wird sichergestellt, dass das Material gleichmäßig verteilt und die gewünschte Konsistenz erreicht wird, die für den weiteren Prozess entscheidend ist.
- Zugabe von Farben und Additiven: Während des Homogenisierungsprozesses können Farben und spezielle Additive zu dem Kunststoffgemisch hinzugefügt werden. Farben werden entweder in Form von Farbpigmenten oder Masterbatch (Kunststoffgranulat mit hohem Farbanteil) zugegeben, um die gewünschte Farbgebung zu erreichen. Zusätzlich können Additive wie Stabilisatoren, UV-Filter oder Antistatika eingearbeitet werden, um spezifische Materialeigenschaften zu verbessern. So wird sichergestellt, dass das fertige Bauteil beständige und widerstandsfähige Oberflächen hat und den Anforderungen der Anwendung entspricht.
- Formaufbau und Kühlung der Form: Die Spritzgussform, oft aus Stahl oder Aluminium, besteht aus zwei Hälften – der sogenannten Düse und der Matrize. Die Form ist präzise gestaltet und bildet die Negativform des zu produzierenden Teils ab. Die Form enthält oft komplexe Einsätze und Auswerfermechanismen, um das Bauteil nach dem Aushärten zu entnehmen. Ein entscheidender Aspekt der Form ist das Kühlsystem: Die Form wird häufig durch Wasserkanäle gekühlt, die den Kunststoff kontrolliert abkühlen. Dabei bedeutet „Kühlen“ jedoch nicht, dass die Form besonders kalt sein muss – die Temperaturen liegen für die Kühlung oft zwischen 20 Grad für Kunststoffe im niedrigen Temperaturbereich wie Polypropylen bis zu Kühltemperaturen von 120 Grad Celsius oder mehr z.Bsp für PA oder PEAK, um die gewünschte Aushärtung des Kunststoffs zu erreichen, ohne den Prozess unnötig zu verlangsamen.
Kühlphase und ihre Bedeutung für die Prozesszeit
Nachdem der Kunststoff in die Form eingespritzt wurde, beginnt die Kühlphase. Diese Phase ist entscheidend, da sie die Aushärtung und Stabilität des fertigen Teils beeinflusst. Die Kühlzeit hängt von verschiedenen Faktoren ab, wie der Größe, Dicke und Komplexität des Bauteils sowie den verwendeten Materialien.
- Individuelle Kühlzeiten für unterschiedliche Teile: Kleinere, dünnwandige Teile benötigen meist kürzere Kühlzeiten, während dickere und komplexere Bauteile längere Kühlzeiten erfordern. Bei der Produktion wird daher die Kühlzeit stets an die spezifischen Anforderungen des Bauteils angepasst. Um ein optimales Ergebnis zu erzielen, muss die Temperatur der Form und die Kühlzeit in einem Gleichgewicht gehalten werden, um Verzug, innere Spannungen und Materialermüdung zu vermeiden.
- Minimierung der Prozesszeit: Um die Produktionseffizienz zu steigern, versuchen Hersteller, die Gesamtprozesszeit zu minimieren. Die Kühlzeit ist oft der längste Abschnitt im Spritzgussprozess, daher sind fortschrittliche Kühlsysteme und optimierte Zykluszeiten wichtige Hebel, um die Produktionskosten zu senken und die Anzahl der hergestellten Teile zu maximieren. Hierbei kommen Techniken wie konturnahe Kühlung, temperierte Wasserkanäle oder Temperiergeräte zum Einsatz, die die Kühlzeit so kurz wie möglich halten und gleichzeitig die Qualität des Bauteils sicherstellen.